Aus Kosten- und Gewichtsgründen (z.B. bei der Entwicklung von Elektrofahrzeugen) wird vermehrt Aluminium als elektrischer Leiter eingesetzt, wobei Kupfer aufgrund seiner mechanischen und elektrischen Eigenschaften nicht vollständig ersetzt werden kann. Eine Kombination dieser beiden Werkstoffe stellt in der Folge eine neue Herausforderungen an die Fügetechnik. Hier erweist sich der Festphasen-Fügeprozess Rührreibpunktschweißen (Abbildung 1) als zunehmend nützlich [1]. Allerdings existieren bei diesem Fügeverfahren, ähnlich zu anderen Fertigungsprozessen, Defizite in der echtzeitnahen Qualitätsprüfung. Der Druck der Automobilhersteller auf die Qualitätsanforderungen macht eine 100% Prüfung in naher Zukunft unabdingbar. Eine mögliche Überwachung des Prozesses durch intelligente Kombinationen von Sensoren und anschließender Auswertung mittels Machine-Learning-Algorithmen ermöglicht nicht nur die echtzeitnahe Qualitätskontrolle, sondern auch das Erkennen und Zuordnen von Fehlern und somit eine direkte Rückkopplung zur gesamten Fertigungskette [2].
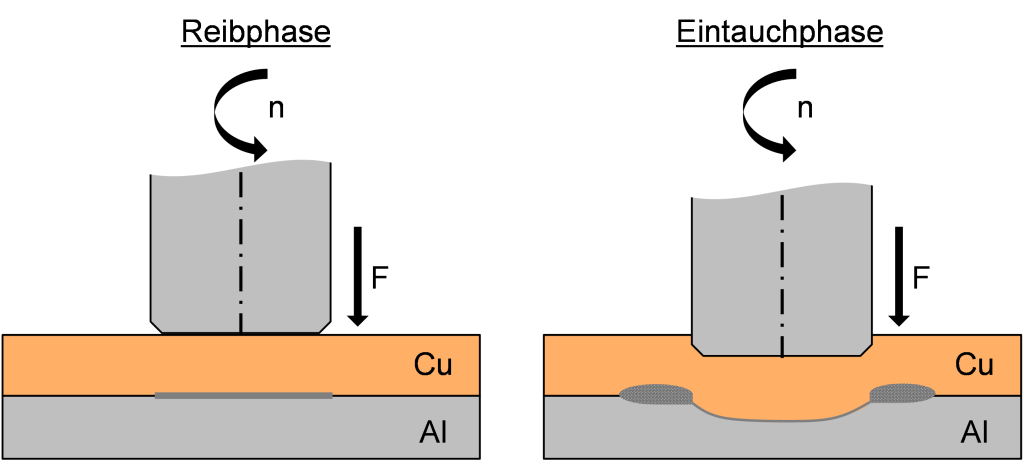
Ziel des Vorhabens ist es, mithilfe eines multisensorischen Ansatzes die spezifischen Prozessgrößen wie Drehmoment, Eintauchweg, Kraft und Drehzahl mit akustischen Prozessemissionen zu kombinieren. Der Sensorkombination schließt sich die Erzeugung realer Experimentdaten an. So können praxisrelevante Prozessunregelmäßigkeiten erzeugt werden. Insbesondere der Werkzeugverschleiß der Reibwerkzeuge wurde als maßgeblicher Einflussfaktor identifiziert und exemplarisch untersucht. Mittels überwachten Lernens wurde in einem ersten Schritt analysiert, inwiefern die ermittelten Prozessdaten zur Erkennung von verschlissenen Werkzeugen und der damit einhergehend abnehmenden Verbundfestigkeit geeignet sind. Die Bewertung der resultierenden Verbindungseigenschaften erfolgte durch Scherzugversuche (Abbildung 2) und metallografische Untersuchungen.
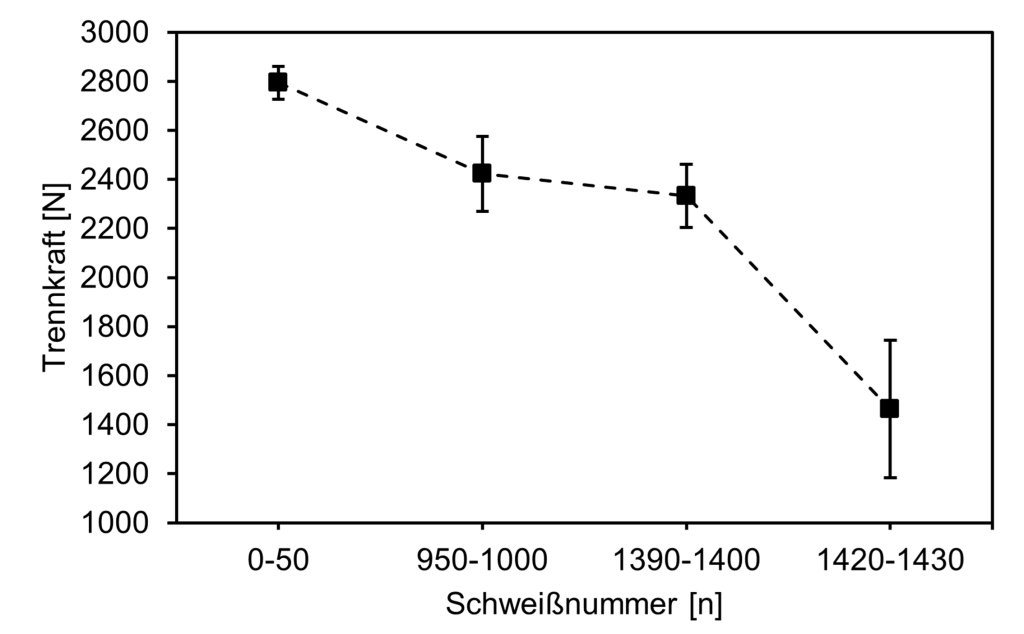
Die Analyse der Scherzugversuche zeigt einen deutlichen Zusammenhang zwischen der Anzahl an Schweißungen und der maximal erzielten Trennkraft. Für eine Abwägung des Werkzeugverschleißes erwiesen sich die intern erfassten Daten des Drehmoments, sowie der Schweißzeit als am aussagekräftigsten (Abbildung 3).
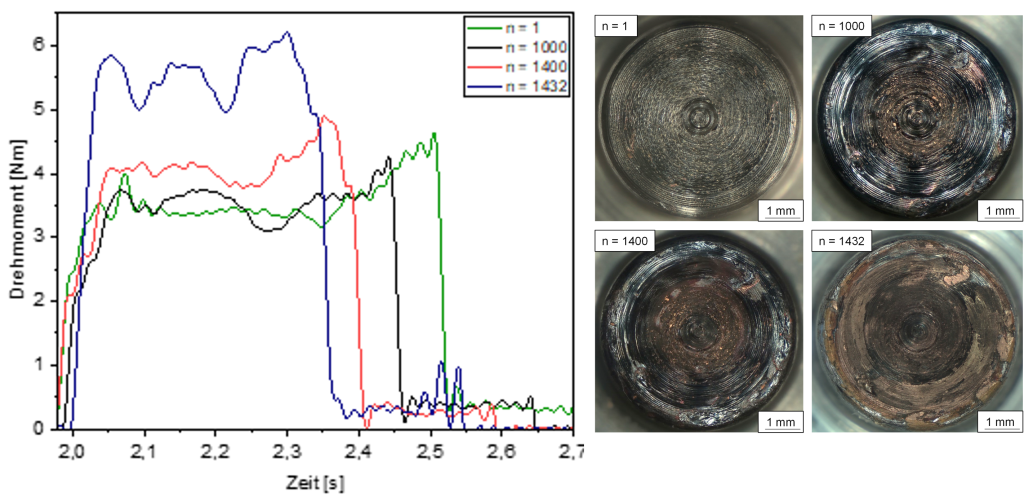
Grundsätzlich zeigen sich in den gefilterten Verläufen zwei Effekte. Der Anstieg des Drehmoments mit zunehmender Schweißanzahl lässt sich auf die geänderten Reibbedingungen zwischen Werkzeug und Kupferoberfläche aufgrund von Anhaftungen an der Reibfläche zurückführen (Abbildung 3). Zum anderen resultiert durch diesen Effekt ein schnelleres Eindringen des Werkzeuges in das Kupferblech, wodurch wiederum die Soll-Eintauchtiefe in kürzerer Zeit erreicht und so die Gesamtprozesszeit verringert wird. Dies wiederum führt zu einem unzureichenden Wärmeeintrag und in der Folge zu einer schlechteren Verbindung zwischen Aluminium und Kupfer.
Anschließend sind die aufbereiteten Daten genutzt worden, um damit den KI-Algorithmus (Neuronales Netz) zu trainieren. Wie bereits vorher beschrieben, wurde als Eingabewert der Drehmomentverlauf verwendet. Als Ausgabe- oder Vorhersagewert wurde die Trennkraft der Schweißverbindung herangezogen. Mihilfe des so trainierten neuronalen Netzes können in der Folge die resultierenden Trennkräfte anhand des Drehmomentverlaufes vorhergesagt werden. Dies ermöglicht einen Punktgenauen Werkzeugwechsel, verhindert so NIO-Verbindungen zum Ende des Werkzeuglebenszyklus und senkt langfristig den Ausschuss durch zerstörende Qualitätsprüfung. Eine weitere Anwendungsmöglichkeit der am Drehmomentverlauf trainierten neuronalen Netze kann beispielsweise die Detektion von Verunreinigungen auf der Bauteiloberfläche (Öle oder Schmierstoffe) im Fügeprozess sein [2]. Im Rahmen des Forschungsvorhabens werden im nächsten Schritt Ansätze der Detektion von Prozessunregelmäßigkeiten auf Grundlage akustischer Prozessemissionen durch ein neuronales Netz untersucht. Die zu entwickelnde KI-Gestützte Prozessüberwachung ist nicht an bestimmte Hersteller von Rührreibpunktschweißmaschinen gebunden und soll nachrüstbar sein. Das Pilotprojekt „In-situ-Qualitätskontrolle“ ist Teil des vom Land Thüringen und dem Thüringer Zentrum für Lernende Systeme und Robotik (TZLR) geförderten „thurAI“ Projekts.
Für weitere Informationen oder Workshops zu diesem oder weiteren Projekten der Ilmenauer Fertigungstechnik (IFt) und des ProKI-Ilmenau wenden Sie sich gern an unsere wissenschaftlichen Mitarbeiter Kai Ehlich oder Maximilian Rohe.
Quellen
[1] Zlatanovic D., Balos S., Bergmann J., Köhler T., Grätzel M., Sidjanin L., and Goel S. (2020). An experimental study on lap joining of multiple sheets of aluminium alloy (aa 5754) using friction stir spot welding. The International Journal of Advanced Manufacturing Technology, 107 (7), 3093–3107.
[2] Köhler T., Schiele M., Glaser M., Schricker K., Bergmann J., Augsburg K. (2020). In-situ monitoring of hybrid friction diffusion bonded EN AW 1050/EN CW 004A lap joints using artificial neural nets. Proceedings of the Institution of Mechanical Engineers. Journal of Materials, Design and Applications. 234 (5), 766–785.
[3] Regensburg A., (2021). Hybrid Friction Eutectic Bonding (HFEB) – stoffschlüssiges Fügen von Aluminium und Kupfer unter Nutzung der eutektischen Reaktion. Fertigungstechnik – aus den Grundlagen für die Anwendung: Schriften aus der Ilmenauer Fertigungstechnik. Universitätsverlag, Ilmenau.