Laserstrahlschweißen ist häufig die Technik der Wahl für eine Vielzahl von industriellen Fertigungsprozessen. Um qualitativ hochwertige Schweißnähte zu erzeugen, verlassen sich die Hersteller oft auf schwere und teure Spannsysteme. Diese begrenzen die Bewegung des Blechs während des Schweißvorgangs und limitieren die Entstehung von Fügespalten. Dies kann die Qualität der Schweißnaht stark beeinträchtigen und erfordert manuelle Anpassungen, sollte sich die Geometrie des zu verarbeitenden Werkstückes ändern.
Das vorrichtungsfreie Schweißen bietet eine kostengünstige und flexible Alternative zu herkömmlichen Spannsystemen. Um dies zu ermöglichen, muss der entstehende Fügespalt erkannt werden.
Eine Möglichkeit für die Erkennung des Fügespaltes bieten langwellige Infrarotkameras.
Diese zeichnen den abgestrahlten Temperaturgradienten von der Oberfläche der Bleche auf. Die Entwicklung des Gradienten kann so anhand einer Videosequenz über die Zeit abgebildet werden. Mithilfe dieser Abbildung kann die Entwicklung des Fügespaltes vorherzusagt und Schweißnahtabbrüche frühzeitig erkannt werden.
In diesem Blogpost werden wir unsere Methode vorstellen, wie der Verlauf des Schweißprozesses anhand von LWIR-Kameras vorhergesagt werden kann. Hierfür werden wir verschiedene Verfahren des maschinellen Lernens miteinander kombinieren und im Weiteren näher betrachten.
Problemstellung
Die Vorhersage von Videosequenzen ist oftmals ein kosten- und zeitintensiver Prozess, der eine Vielzahl von Trainingsdaten benötigt. Dies führt insbesondere bei zeitkritischen und kostenintensiven Prozessen, wie zum Beispiel Laserstrahlschweißen, zu mehreren Problemen. Zum einen ist es teuer, fehlerhafte Schweißnähte und somit Trainingsdaten zu erzeugen, zum anderen muss die Vorhersage schnell erfolgen.
Anhand dieser Limitierungen ergeben sich folgende Anforderungen an die entwickelte Methodik des maschinellen Lernens:
- Reduktion der Dimensionalität von Videosequenzen auf ein Minimum
- Vorhersage des weiteren Verlaufs des Schweißprozesses
- Frühzeitige Detektion von Schweißnahtfehlern
Um diese Anforderungen zu erfüllen, teilen wir das KI-Modell in drei Module ein, welche jeweils eines der hier genannten Probleme lösen können.
Autoencoder – Dimensionsreduktion
Um die Dimension der Inputdaten zu reduzieren, bietet sich ein sogenannter Autoencoder an. Ein Autoencoder ist ein besonderes KI-Modell welches lernt Eingabedaten auf ein Minimum nötiger Merkmale zu reduzieren. Anhand des minimalen Merkmalsraums wird im Anschluss die Eingabe rekonstruiert. Dies ist in Abbildung 2 veranschaulicht.
Die Rekonstruktion und die ursprüngliche Eingabe werden miteinander verglichen, um zu überprüfen, wie viele Informationen durch die Dimensionsreduktion verloren gegangen sind. Je niedriger der Verlust, desto besser repräsentiert der minimale Merkmalsraum die Eingabedaten.
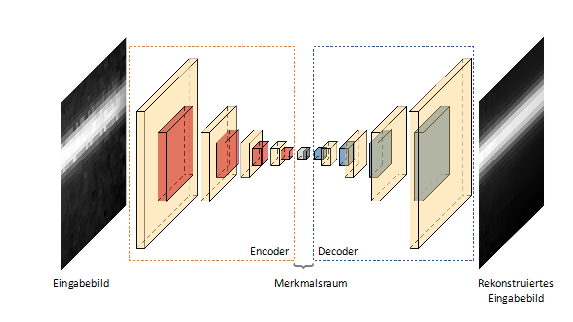
Abbildung 1 Beispiel Autoencoder [1].
Für die Vorhersage des weiteren Schweißprozesses, ist jedoch ausschließlich der reduzierte Merkmalsraum von Interesse, da alle relevanten Merkmale hier enthalten sind. Beispielhaft ist in Abbildung 2 dargestellt, wie eine Videosequenz auf 16 Merkmale reduziert wird.
Abbildung 2 Dimensionsreduktion einer Videosequenz auf 16 Merkmale.
Der Schweißnahtabbruch ist in der Abbildung rot markiert und durch eine Änderung des Verlaufs deutlich sichtbar.
Der Autoencoder löst somit die erste Anforderung an unsere Methodik.
Rekurrentes Netwerk – Vorhersage
Rekurrente Netzwerke eignen sich besonders gut für die Verarbeitung und Vorhersage von Zeitreihen. Durch die Dimensionsreduktion des Autoencoders erhalten wir eine Zeitreihe mit 16 Merkmalen. Diese eignet sich als Eingabe für ein rekurrentes neuronales Netzwerk und kann somit für die Vorhersage des weiteren Schweißprozesses verwendet werden.
Um die Vorhersage zu realisieren, ist es zuerst notwendig, Informationen über den Prozess zu sammeln bzw. Wissen aufzubauen. Dieses Wissen wird vom rekurrenten Netzwerk verwendet, um den nächsten Zeitschritt vorherzusagen. Die vorhergesagte Ausgabe wird dann erneut als Eingabe verwendet, um einen weiteren Zeitschritt vorherzusagen. Diese autoregressive Vorhersage wird n-Mal wiederholt, bis der restliche Verlauf vorhergesagt ist. Dieser Ablauf ist in Abbildung 3 visualisiert.
Abbildung 3 Autoregressive Vorhersage des Schweißprozesses.
Durch das so erhaltene Wissen kann der Autoencoder nun ein Bild an der Stelle t+n rekonstruieren und somit Aufschluss über mögliche Fehler im weiteren Verlauf geben. Abbildung 4 zeigt dies beispielhaft.
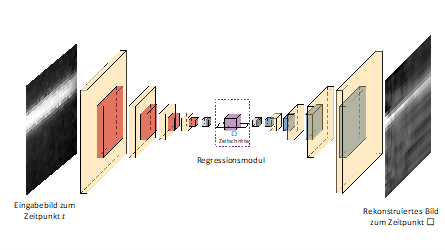
Abbildung 4: Erweiterung des Autoencoders durch ein rekurrentes Netzwerk [1].
Eine Kombination aus Autoencoder und rekurrentem Netzwerk löst somit die 2. Anforderung an unser Modul.
Multi-Layer-Percepton – Detektion
Im letzten Schritt ist es notwendig, die vorhergesagten Merkmale zu klassifizieren. Dies könnte zum Beispiel anhand der rekonstruierten Bilder (siehe Abbildung 4) geschehen. Da das rekonstruirte Bild jedoch lediglich eine Übersetzung der Merkmale in menschlich verständliche Informationen ist, kann die Transformation von vorhergesagten Merkmalen zu einem Bild übersprüngen werden. Die Detektion von Fehlern findet ausschließlich basierend auf den vorhergesagten Merkmalen statt.
Das Modell wird durch ein Multi-Layer-Perceptron (MLP) erweitert, um fehlerhafte Abschnitte im Schweißverlauf zu detektieren.
Das vollständige Modell ist in Abbildung 5 dargestellt.
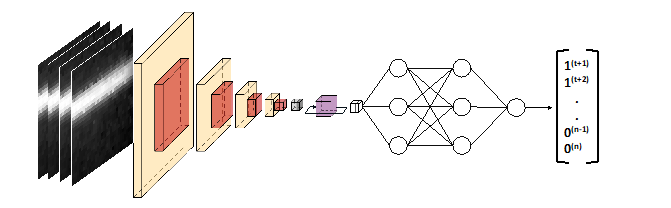
Abbildung 5: Entwickeltes Modell [1].
Jeder vorhergesagte Zeitschritt wird durch das MLP analysiert und klassifiziert. So kann erkannt werden, ab welchem Zeitpunkt die Schweißnaht fehlerhaft ist.
Durch die Kombination der vorgestellten Modelle, kann auch die dritte Anforderung an unsere Methodik erfüllt werden.
Ergebnis
Das entwickelte Modell ist in der Lage, den Schweißnahtabbruch vorherzusagen. Allerdings weichen der vorhergesagte Abbruch und der tatsächliche Abbruch ab.
Dies ist zu erwarten, da keines der vorgestellten Modelle fehlerfrei funktioniert und die Detektion damit beeinträchtigt wird. In Abbildung 6 ist das Ergebis einer Detektion aufgezeigt. In diesem Beispiel unterscheiden sich der vorhergesagte Schweißnahtabbruch und der tatsächliche Schweißnahtabbruch lediglich um 3 mm.
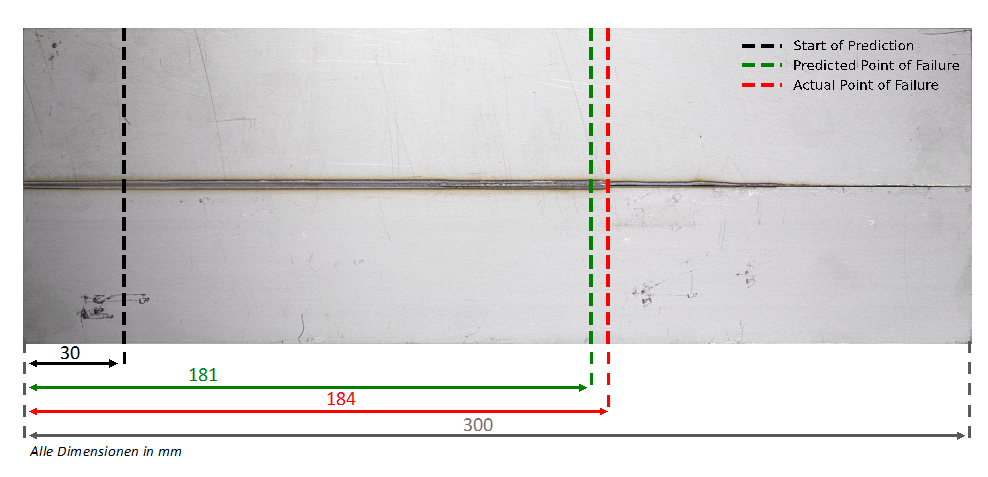
Abbildung 6 Ergebnis vorhergesagter Schweißnahtabbruch [1].
[1] Walther, D., Junger, C., Schmidt, L., Schricker, K., Notni, G., Bergmann, J. P., & Mäder, P. (2024). Recurrent Autoencoder for Weld Discontinuity Prediction. Journal of Advanced Joining Processes, 100203.
Beitrag von: Dominik Walther